About TST Tooling SOftware
Our Mission: TST Software will exceed customer expectations by providing complete solutions from start to finish- solutions that make sense.
TST Tooling Software Technology, LLC is the global leader among service providers in the international market. Our world class applications and stellar service provide our clients the competitive edge necessary to be successful in today’s business environment.
Headquartered in Clarkston, Michigan, we provide solutions that make sense from start to finish. TST Tooling Software Technology is known for its innovative cutting edge CAD/CAM/CAE software, support services, and Tool Shop Tracking software developed specifically for the Mold, Die and Secondary Machining Industries.
At TST, our mission and commitment is to provide the COMPLETE hardware and software SOLUTION for the Tooling Industry. We manage your data from the time it comes in, to the time it leaves the building, saving you both time and money. Our broad and complementary range of technologies and knowledge starts with reading your part files, analyzing costs and materials, proceeds to design, includes machining and molding, works on the shop floor, and returns information to your clients.
“We promise to promptly recognize our clients’ needs and provide the highest level of customer satisfaction possible for your company’s continued growth and success.”
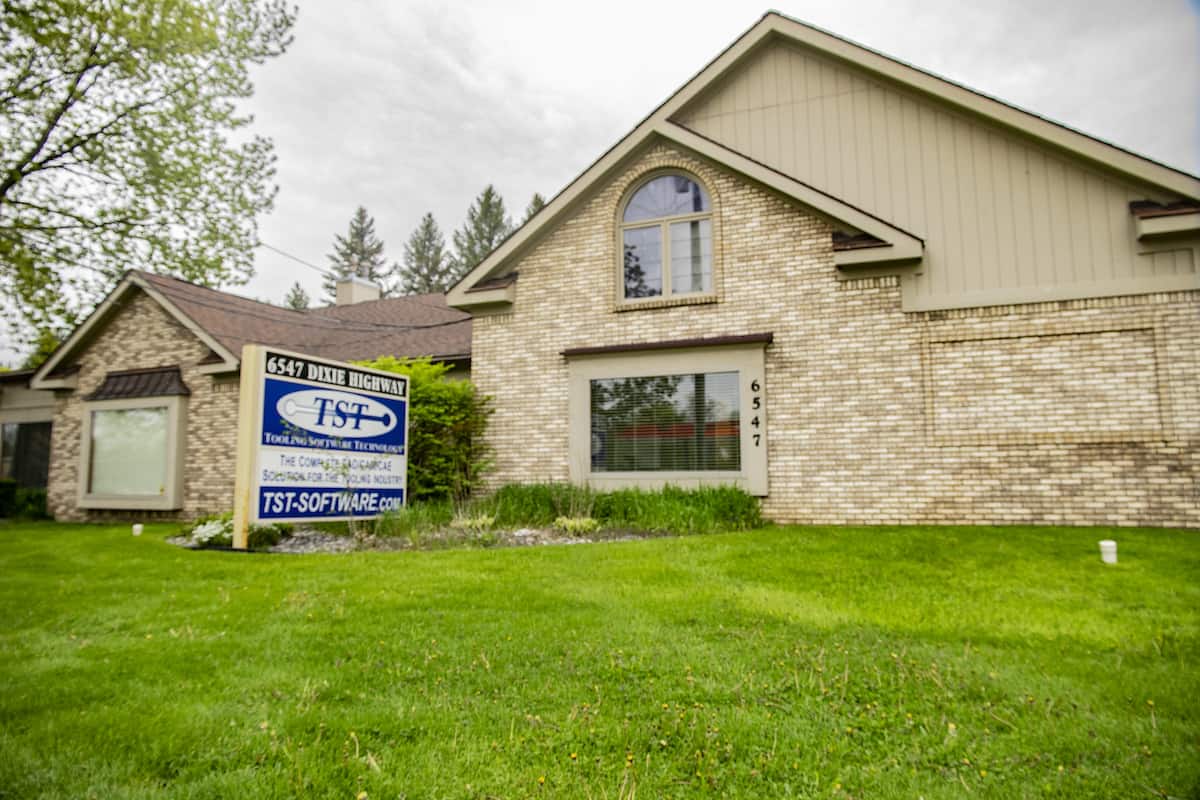
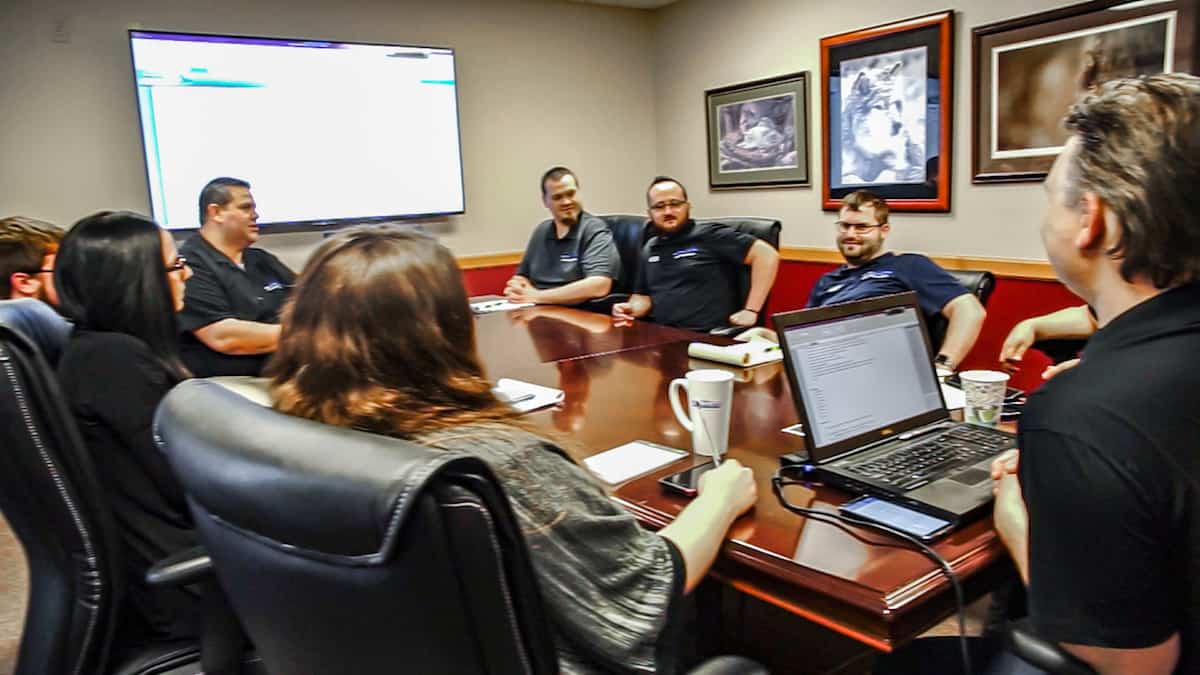